The Alcast Company Ideas
The Alcast Company Ideas
Blog Article
The Basic Principles Of Alcast Company
Table of Contents10 Simple Techniques For Alcast CompanyThe 3-Minute Rule for Alcast CompanySome Known Incorrect Statements About Alcast Company The Alcast Company StatementsIndicators on Alcast Company You Need To KnowGetting The Alcast Company To Work
The refined distinction hinges on the chemical content. Chemical Contrast of Cast Aluminum Alloys Silicon promotes castability by lowering the alloy's melting temperature and boosting fluidness throughout spreading. It plays a vital function in permitting elaborate molds to be loaded properly. Additionally, silicon adds to the alloy's stamina and use resistance, making it beneficial in applications where toughness is critical, such as automotive components and engine components.It also improves the machinability of the alloy, making it less complicated to refine into completed products. In this means, iron adds to the general workability of aluminum alloys.
Manganese adds to the stamina of aluminum alloys and boosts workability (aluminum metal casting). It is generally used in wrought light weight aluminum products like sheets, extrusions, and profiles. The presence of manganese help in the alloy's formability and resistance to fracturing during fabrication processes. Magnesium is a light-weight element that offers strength and influence resistance to light weight aluminum alloys.
Not known Factual Statements About Alcast Company
Zinc boosts the castability of aluminum alloys and helps manage the solidification procedure throughout casting. It boosts the alloy's stamina and firmness.
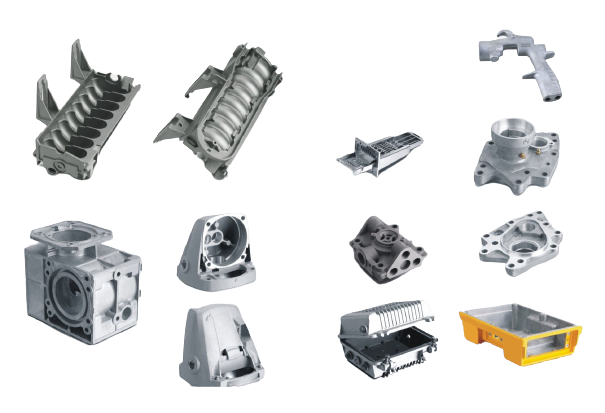
The key thermal conductivity, tensile toughness, return toughness, and prolongation differ. Amongst the above alloys, A356 has the highest thermal conductivity, and A380 and ADC12 have the lowest.
Not known Factual Statements About Alcast Company
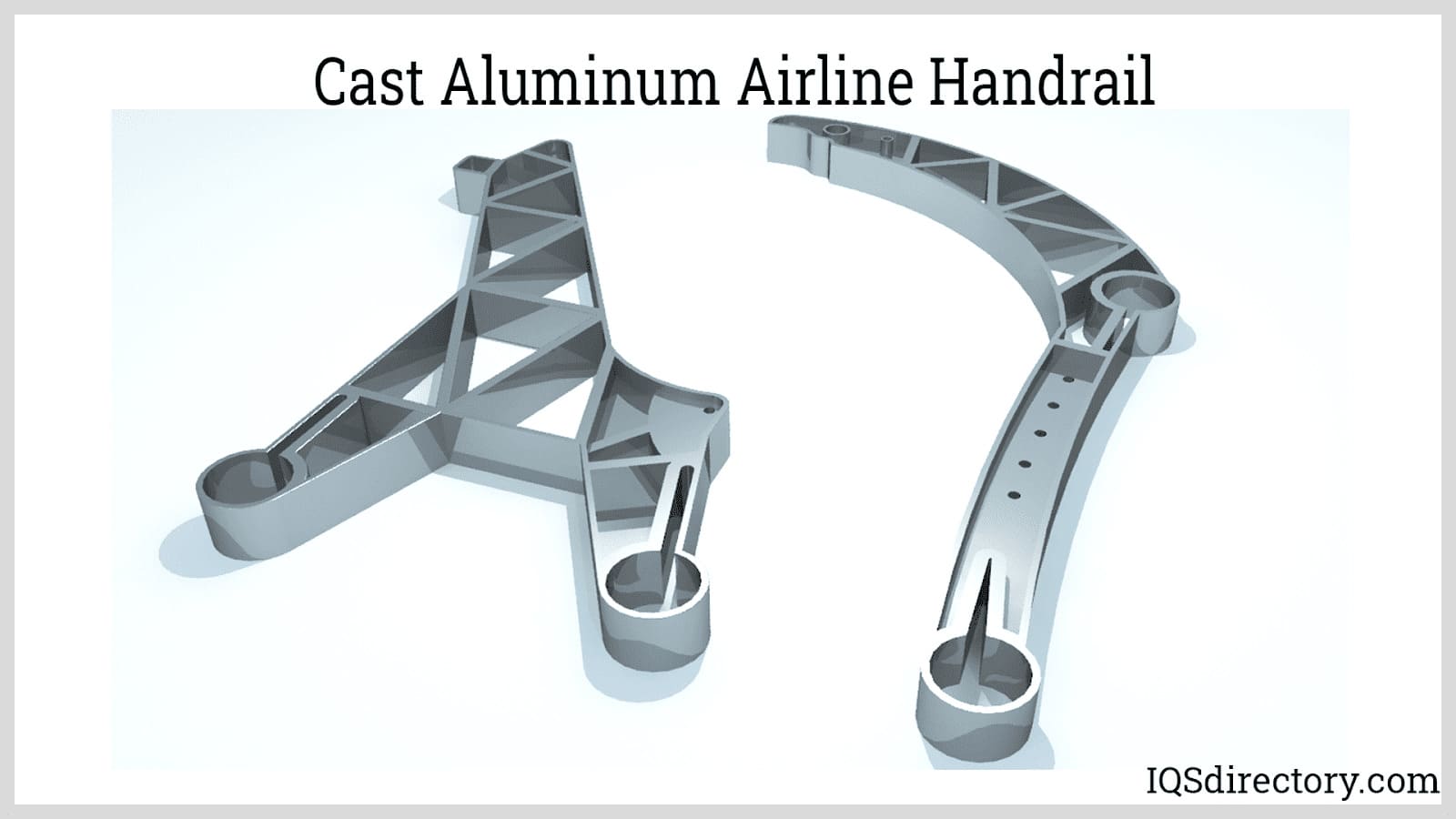
In accuracy casting, 6063 is fit for applications where elaborate geometries and high-grade surface area coatings are extremely important. Examples include telecommunication units, where the alloy's premium formability enables for smooth and cosmetically pleasing designs while preserving structural honesty. In a similar way, in the Illumination Solutions industry, precision-cast 6063 parts create elegant and effective lighting fixtures that require complex shapes and excellent thermal performance.
It results in a better surface area coating and better corrosion resistance in A360. Furthermore, the A360 displays remarkable prolongation, making it excellent for complex and thin-walled elements. In precision spreading applications, A360 is fit for industries such as Consumer Electronics, Telecommunication, and Power Tools. Its improved fluidity permits elaborate, high-precision elements like smartphone casings and interaction tool housings.
Everything about Alcast Company
Its special homes make A360 a beneficial choice for accuracy casting in these sectors, boosting product toughness and top quality. Aluminum Castings. Aluminum alloy 380, or A380, is an extensively made use of casting alloy with several unique qualities.
In precision casting, aluminum 413 beams in the Customer Electronic Devices and Power Devices sectors. This alloy's remarkable corrosion resistance makes it an excellent choice for outside applications, making sure resilient, resilient products in the mentioned markets.
Get This Report about Alcast Company
The light weight aluminum alloy you choose will significantly impact both the casting process and the residential properties of the last item. Due to the fact that of this, you need to make your choice carefully and take an educated method.
Figuring out the most appropriate aluminum alloy for your application will certainly indicate evaluating a large array of attributes. The initial group addresses alloy moved here qualities that affect the production process.
What Does Alcast Company Do?
The alloy you select for die spreading straight influences numerous elements of the casting process, like how very easy the alloy is to deal with and if it is vulnerable to casting problems. Hot fracturing, likewise referred to as solidification cracking, is a regular die casting issue for light weight aluminum alloys that can result in internal or surface-level tears or cracks.
Certain aluminum alloys are a lot more vulnerable to warm splitting than others, and your choice ought to consider this. Another common issue discovered in the die casting of light weight aluminum is pass away soldering, which is when the actors adheres to the die walls and makes ejection difficult. It can harm both the actors and the die, so you must try to find alloys with high anti-soldering properties.
Rust resistance, which is already a notable feature of light weight aluminum, can vary significantly from alloy to alloy and is a necessary characteristic to take into consideration depending on the environmental conditions your item will certainly be exposed to (aluminum foundry). Put on resistance is an additional residential or commercial property typically sought in aluminum products and can differentiate some alloys
Report this page